Do these five steps, printing production efficiency is instantly improved
Time:2024-04-02
Views:1755
Prepress
1. Quality control of pre-press graphics
The text on the original manuscript should not contain miswords and wrong words, and the text input personnel should work carefully. Otherwise, if the machine personnel find mistakes and missing characters in the printing, it is necessary to stop printing, which is bound to cause waste and seriously affect production efficiency.
2. Rationality of layout design
Designers should pay attention to the following when designing the layout:
Designers should reasonably design colors or use spot colors to meet customer requirements and improve the production efficiency of the printing press. Try to avoid the appearance of hollow words more than two colors, otherwise it is difficult to achieve the ideal registration state, which brings a lot of trouble to printing; Designers should be familiar with the characteristics of different papers, and be able to adjust the color according to different papers, so that the color can be more quickly and achieve the purpose of improving production efficiency.
3. Layout
In the process of typesetting, the typesetting staff must be careful and need to have a high professional quality. In addition, the proofreading process after typesetting the manuscript is essential to ensure the high quality of the prepress process. Generally, different personnel are required to perform the first and second proofreading work twice to ensure that the content of the film issued or the content of the CTP version is correct. Otherwise, even if there is a little mistake, if the machine personnel do not see it, it will cause the whole batch of live parts to become waste products, resulting in serious quality accidents.
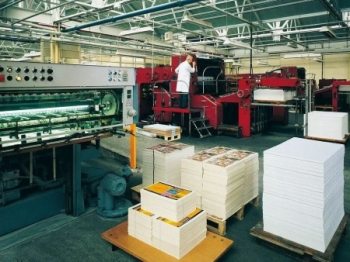
High quality printing materials
The quality of raw materials is very important to improve the quality of printing products and production efficiency. This paper mainly introduces the impact of plate material, paper and ink on printing production efficiency and the corresponding precautions.
1. Plate material
The plate making workshop should carefully read the plate printing task list issued by the workshop and seriously complete their work.
When printing, plate making personnel should pay attention to the following matters: for the film must pay attention to the accuracy of the printing, before exposure must be vacuumed, otherwise there will be an inaccurate case, which requires re-printing, not only will extend the waiting time of the printing press, but also waste the PS plate, resulting in reduced printing production efficiency; For the flat network or shallow network more live parts, to strictly control the exposure time, to minimize the loss of the network, but also pay attention to the phenomenon of "network deficiency", dirty points.
Generally, dirty points occur the most in the printing process, and many printing personnel only care about their own printing speed, and do not seriously repair dirty, resulting in too long time to stop repairing dirty in the printing process.
Therefore, the strict requirements for the printing process is a prerequisite for improving the printing production efficiency, the printing workshop must be strict requirements for the plate making department, and strive to ensure that there are no dirty points on the plate, no defects such as dot deficiency, and ensure the quality of the printing plate.
2. Paper
Paper is one of the main raw materials for printing production, and its quality has a great impact on the quality of printing. The paper cutting department should carefully read the paper cutting task list issued by the printing workshop, and communicate with the printing workshop in time for the questions, because the paper cutting error will cause a lot of losses, when there is more work and a wide variety of paper, the paper cutting personnel should strengthen the sense of responsibility, ensure the quality of the cutting paper, ensure the cutting blade, the cutting paper neatly, accurately, and without paper wool. Otherwise, if the size of the paper is different, the paper can not be smoothly printed, the printing speed can not be raised, and the production efficiency will naturally decline; If the paper is not smooth, the paper will not run smoothly, resulting in slow printing speed and low efficiency; If the knife is blunt, the paper hair cut out is too much, it is easy to lead to ink spots in the printing process, resulting in printing downtime, seriously affecting the printing quality and production efficiency. Generally, the cut paper must be wrapped with plastic film to avoid the paper being placed for too long and deformed.
3. Ink
In the printing process, the failure caused by the ink is very frequent, which greatly reduces the printing production efficiency and printing quality. For example, ink is unavoidable in the offset printing process, which often appears in the field and ink heavy parts, once it occurs, it usually needs to stop processing, if the long version of the live stop more, the speed does not go up, the output will definitely be affected; If the short version of the live shutdown times, it is difficult to ensure that the ink color is consistent, resulting in a significant decline in the quality of the live parts. Therefore, when the operator encounters such problems, it is necessary to carefully observe, think more, analyze the reasons and deal with them in time, and cannot blindly shut down the ink skin, which in most cases is related to the performance of the ink, for example, in the cold winter, if the appropriate additives increase the fluidity of the ink, it can reduce the ink skin. In addition, it is best to choose high-quality ink printing, in general, the quality of imported ink is more stable, ink cover failure is relatively less, suitable for long-term use, can improve printing production efficiency.
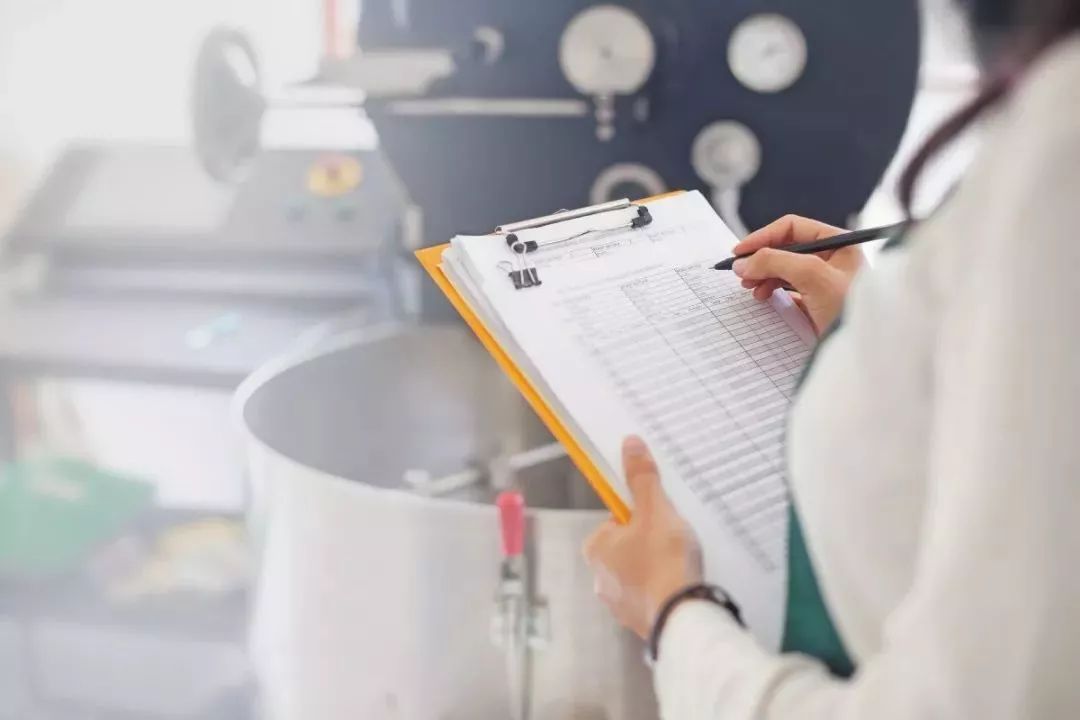
Reasonable arrangement of production
The production arrangement of the printing workshop must be performed by a person who knows printing, is familiar with the printing process and has rich printing experience. Only in this way can we reasonably arrange production tasks, make full use of the production capacity of the printing press, and improve production efficiency. When arranging production tasks, pay attention to the following matters.
1. Print the same amount of paper together
When printing thick paper, the tooth row is stretched, and the spring pressure is large. After printing the live parts of thick paper, the force of the tooth row paper suddenly decreases, and the spring pressure will also decrease. Such frequent increase and reduction of the spring pressure and the tooth row paper intensity will cause damage to the tooth row and affect the overprinting accuracy of the printing press. Therefore, general printing companies in the arrangement of production tasks, to try to arrange the thick paper live parts in a printing machine, the thin paper live parts in another printing machine, if there is only one printing machine, you need to add a paper quantity moderate in the middle of the thick paper live parts and thin paper live parts, so that the teeth of the paper has a certain buffer, but also to avoid frequent adjustment of the printing machine. Resulting in reduced production efficiency.
2. Print the same size parts together
Printing the same size of the live parts together can avoid each printing of the live parts, the rules of the paper feed and receiving parts, the size of the ink mixing area, etc., both to reduce waste and improve production efficiency.
3. Print the parts with similar ink color together
The ink color is close to the live parts are printed together, so that after changing the live parts, you do not have to spend a lot of time running the ink, and sometimes you only need to walk once over the plate paper to run the ink, which improves the printing speed and saves time.
4. Print first according to the sample printing, and print after the customer‘s signature
A lot of live parts need customers to follow the machine to fix the color, and sometimes the ink color runs well, but also need to wait for customer confirmation, spending a lot of time. Therefore, it is generally necessary to print the living parts that do not require the customer to follow the machine first, and the simple living parts should be printed out.
In short, how to formulate production tasks should be based on the experience of the pilot and the situation of the specific parts. The captain should read the production task sheet carefully, be clear about the specific requirements of the live parts, and make preparations in advance, so as to maintain high quality and efficient printing.
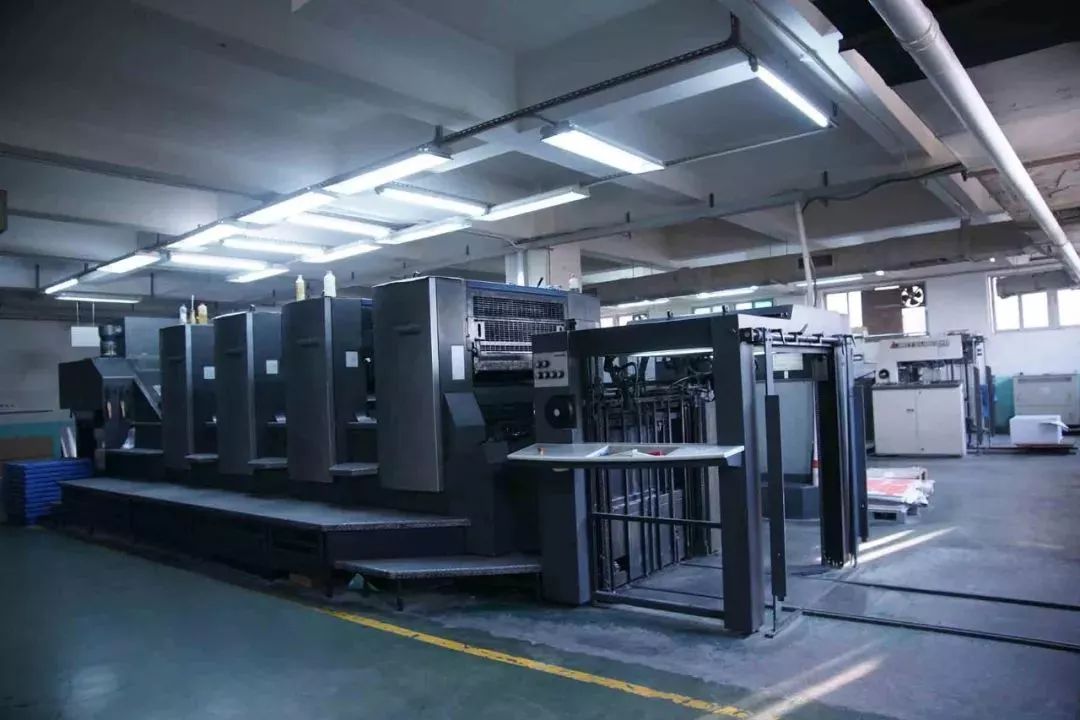
Ambient temperature and humidity
High or low temperature and humidity have a particularly large impact on the printing of live parts. Especially in map printing, because there are more two-color and three-color lines and small text on the map, and there are three-color or four-color color markers around each printing sheet, the accuracy requirements are particularly high, which requires that the temperature and humidity must meet the printing regulations when printing.
If the humidity is low, the paper will be deformed after absorbing the water on the printing plate when it is turned on, even if the first color group changes little, the paper absorbs a lot of water when it is printed to the fourth color group, which will cause the left and right rules and the upper and lower rules to be unable to fit together. In this case, it can not be printed, and it can only be printed after the paper is dried in the paper drying room until the humidity is moderate, which has a great impact on the printing production efficiency. And if it is a quantitative of 105g/m2 of paper, sometimes only the method of paper change can be taken, which will cause huge economic losses to the workshop.
Therefore, when the humidity is low, it is necessary to open the humidifier to increase the humidity to 60% to 70% in order to print the map.
When the temperature is low, the ink can not be transferred to the paper well due to its large viscosity, which will lead to slow printing speed; When the temperature is high, the fluidity of the ink will increase with the increase of temperature, which is not conducive to printing. This requires the captain to take over or go to work in the morning each time (especially in the autumn and winter season, the machine roller temperature is low), be sure to control the temperature and humidity of the workshop according to seasonal changes, the general printing workshop should be equipped with humidifiers and air conditioning equipment, the temperature is controlled between 18 ~ 23 ° C, the humidity is controlled at 60% ~ 70%, so as to ensure the normal operation of the printing press. Improve printing production efficiency.
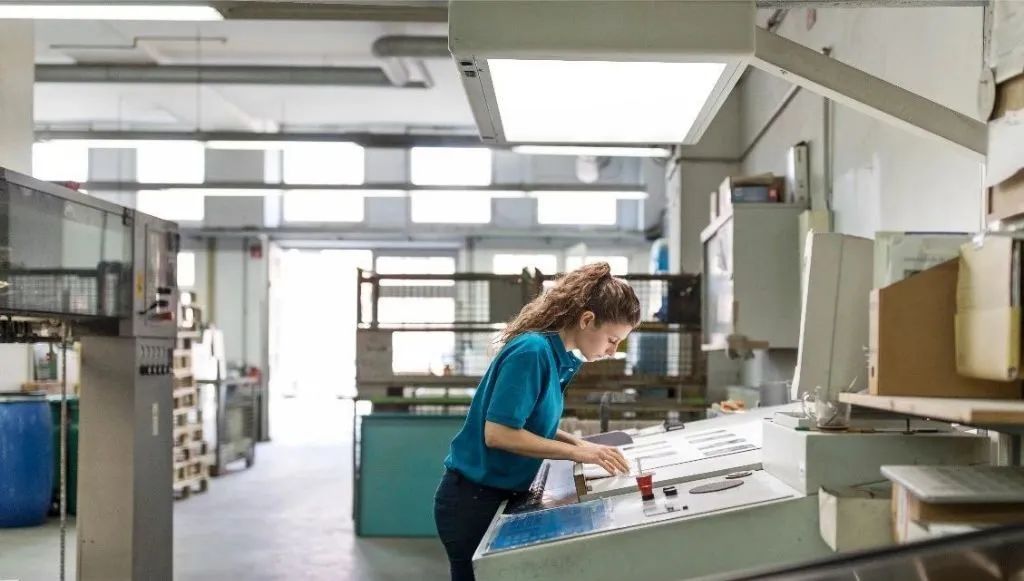
The solidarity of the printing crew
1. Requirements for the captain
The printing captain must not only have excellent printing technology level, but also must have a high sense of responsibility in the printing process. The technical and comprehensive quality of a pilot will directly affect the efficiency of printing production, and the general captain needs to have the following qualities.
First, the captain must establish a master‘s attitude, be responsible for each work he does, think carefully about where to pay attention to each work before printing, and then sample frequently in the printing process, look at the signal bar, compare frequently, and look at the ink frequently, to ensure that the ink color of the print is consistent and the print is flawless.
Second, the captain must understand and master pre-press professional knowledge, understand the knowledge of paper, ink, moistening solution, etc., to eliminate possible faults or problems before printing, and take measures to minimize unavoidable faults in advance.
2. Requirements for crew members
Efficient printing production requires a good team. The unity of the crew is conducive to the smooth operation of the captain‘s work. The assistant work fast and agile, can very well assist the captain to do the printing work, the time is short, then the result is that the production efficiency in the printing process is greatly improved.
In combination with the above aspects, the improvement of printing production efficiency not only requires the captain to always pay attention to the influencing factors of all aspects of the printing press, but also requires the coordination and cooperation of many links such as pre-press links and printing materials. Only by grasping the quality from the source, avoiding common drawbacks in every link, ensuring quality and quantity, and connecting with the printing link, can we truly achieve the improvement of printing production efficiency.