Practical solutions to the discoloration problem of Heidelberg printing presses
Time:2025-07-10
Views:97
1- Layout design for printed materials
First of all, we should check whether the design of our printed materials on the layout is reasonable. For instance, placing patterns with a large amount of ink (or the superposition of four-color screens) at the drag position is definitely not conducive to printing high-quality printed materials. We should place them at the gripper position, which is beneficial for the gripper to control the paper. It is easier to print out non-color-changing printed matter.
2- Periphery of the printing press
If the color change of the printed matter has already occurred, we should not immediately conclude that the problem lies with the printing machine itself. Instead, we should first look for the cause on the periphery of the printing machine. We should first use a magnifying glass to observe the dots on the printing plate and check if there has been any dot deformation. If it is found that dot deformation has already occurred on the printing plate, Then we should examine the film to rule out any problems that occurred during the production process.
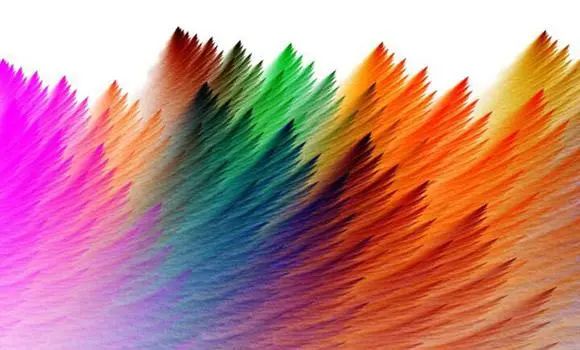
3- The Ink Path System
After we have ruled out the problem with the film, we should check if there is any issue with the ink circuit system. We can use a very simple method to check the ink circuit system. First, we should thoroughly clean the ink circuit with car wash water (water can be added). After parking, we should check if there are any white crystalline particles in the ink circuit. If we find such substances, Then the discoloration that occurs might be caused by the local discoloration of the printed matter due to the accumulation of crystalline substances. This kind of discoloration often more prominently reflects the local color deviation of the brush.
After washing the car, no crystalline substances were found. We restarted the printing machine and injected ink to each ink roller. After the ink injection was completed, we closed the plate support ink roller and the plate support water roller to check if the pressure met the standard. If not, I suggest readjust the pressure of all ink rollers to achieve a better state.
4- Waterway system
After confirming that there are no issues with the ink path system, we should inspect the waterway conditions, adjust the pressure between the plate water roller, metering roller, water bucket roller, and water diversion roller, and pay special attention to adjusting the pressure of the middle roller. Under the condition that our technical skills are insufficient, it is best not to use the middle water roller during the printing process.
5- Rubber blanket
If there are no issues with the ink and water path, we should check whether the rubber blanket is standard. We suggest that the thickness of the blanket should be 35 microns. The rubber blanket is preferably a brand one with aluminum strips and is new. A new rubber blanket is best tightened again after being used for a period of time.
.jpg)
6- Dental pads and dental strips
If the discoloration problem still hasn‘t been solved after all these measures have been taken, then we might need to consider the issue with our teeth. We should clean the dental pads and dental plates, and it‘s best to remove the springs for cleaning. Some manufacturers only know how to clean the dental pads but don‘t know how to clean the dental plates. This is actually incorrect. Check for any dead teeth. Use an efficient rust remover like WD-40 and apply oil to the teeth and dental shafts to ensure there are no dead teeth.
7- Paper
Check the paper feeding condition, which includes the adjustment of the paper feeding air, the flatness of the paper in the front guide, the fit between the paper and the paper press, the operation of the paper feeding belt, etc.
8- Trial printing
After doing all these, we can start the trial printing. When doing the trial printing, it‘s best to choose a better quality coated paper to avoid the impact of paper issues on us. For thin paper, we should set the air volume for embossing as small as possible, and for thick paper, we should set it appropriately larger.
After doing all these, our printed materials may be able to solve the problem of color change. Of course, there are also those that cannot be solved. If our printed materials still change color after all these efforts, please contact a professional service team as soon as possible for repair to solve the problem quickly.