Do these three steps well, post-press processing is guaranteed
Time:2024-04-10
Views:1733
The precision of post-press processing is one of the important indicators to measure the quality of product forming, so how to improve the precision of post-press processing is particularly important. The main factors affecting the accuracy of post-press processing are: the accuracy of post-press processing equipment is reduced, the adjustment of post-press processing equipment is improper, and the paper is stretched and deformed.
Next, to share with you the impact on the post-press processing accuracy of the three main factors, the last one most people did not think of.
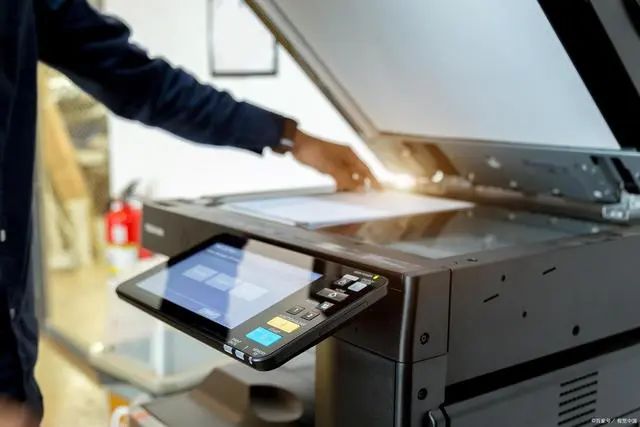
First, equipment accuracy decline
In the post-press processing equipment, the structure of the automatic stamping machine and the automatic die-cutting machine is basically the same, mainly divided into three parts: paper feeding, host and paper receiving; The working principle is basically the same, and the main parts that control the processing accuracy are the left and right gauge position and the front gauge, as well as the paper guide system that helps the printing product position.
After a long time of use, the parts of the machine wear, the accuracy decreases, and the parts of the paper guide system are also affected. In particular, the speed and long time continuous operation of the machine will cause more damage to the tooth rows and the spring of the left and right gauge guide wheel. In the case of high-speed operation for a long time, the tooth plate and the spring repeatedly move to produce higher temperatures, resulting in metal fatigue. In this way, the rigidity of the teeth and the elasticity of the spring decrease, resulting in insufficient pressure of the paper teeth, resulting in the inaccurate positioning of the printed product in the former gauge position.
In order to avoid the accuracy of the stamping machine and die cutting machine caused by the overprinting is not allowed, the equipment should be used rationally, and the machine should not be allowed to run continuously and at extreme speed 24 hours a day, and the speed limit should be set for the factory capacity of the machine. Unprocessed products should keep the machine stationary; At ordinary times, all parts of the machine should be lubricated, and regular maintenance should be carried out on the teeth and paper guide wheel springs.
Second, the machine is improperly adjusted
In the process of hot stamping and die cutting, the pressure of the paper teeth is too small, and the paper edge cannot be gripped, and the paper will slip when embossing. The opening and closing action of the paper delivery teeth and the teeth are out of whack, and some parts of the paper delivery system are out of whack, so that the paper feed is not in place or; Excessive force will lead to inaccurate overprinting. Therefore, when adjusting, attention should be paid to the size of the paper pressure and the amount of paper, especially the pressure of the paper wheel of the paper delivery system, and attention should be paid to the speed from slow to fast when starting.
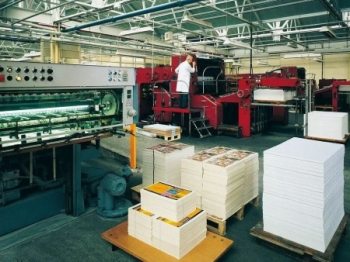
Three, paper deformation
There are two types of paper deformation:
1. Paper cutting is not standard, there are beveled or wavy paper edges. Therefore, it is necessary to ensure that the paper cut out reaches the right Angle and straight edge; Do not beat the edge of the paper repeatedly when cutting, so as not to cause wavy paper edges.
2. The water content of paper is unstable. It is mainly manifested in some processes that require heating, such as UV curing, screen printing drying, hot printing heating, oil drying, etc., and the water content of the paper changes. In order to avoid the deformation of the paper caused by the change of water content, the various processes should be handed over in time, the retention time should not be too long, and certain protective measures should be taken to prevent the natural loss of water in the paper, such as protection with protective film. And keep the workshop temperature, humidity and paper water content balance. For the paper water loss caused by special process heating, it should be compensated by adjusting the temperature and humidity to restore the paper water content to the original standard state.
In fact, there are many reasons for poor post-press processing accuracy, as long as we carefully pay attention to all aspects of the processing process, sum up experience, strictly good operation technology and process technology, we can avoid, many orders have defects, most of them are caused by the lack of attention to details, and it is necessary to pay attention to the details and the practice of high requirements on the process. In order to produce qualified products, we can reduce the product loss rate, improve production efficiency, and slightly better in output and quality control.
The above is to share the professional knowledge about post-press processing, I hope it will be helpful to you.