The secret of printing color difference control
Time:2025-02-14
Views:596
Establish a sound color management system
As we all know, in the printing process to completely avoid color difference is impossible, the key is how to control the color difference within a reasonable range. The first step in the printing process to control the color consistency of the product is to establish a sound color management system, so that the operator knows the standard of qualified products, including the following two points.
1. Determine the upper and lower limits of product color with customers
When we produce a product for the first time, we should develop the standard upper and lower limits of the color of the product, and it is determined as "standard sample" after the customer seal the sample. In future production, the standard color of the standard sample (which can also be the first batch of product samples) is based on it, and the fluctuation of the color can not exceed the upper and lower limits of the standard. That is to say, to confirm the color difference standard range with the customer in advance, to ensure the consistency of product color at the same time, to give the production personnel a reasonable color fluctuation range, making the product color standard more operable. It is not necessary to simply catch up with the batch sample every time you produce, which will lead to the more batches of printing, the more severe the color difference of the product, the difference is as small as a thousand miles.
In addition, it must be noted that the "standard sample" of the customer‘s seal should be replaced regularly, so as not to cause deviation between the standard sample and the actual printed product due to a long time.
2, improve the first and last sample signing, inspection system
If you want to further ensure the implementation of the color standard, the product color inspection items should also be included in the "Product first and last part Inspection System" and "Inspection quality Record", so that the workshop management personnel can control the color differences of the products, and the unsuitable products will not pass. At the same time, workshop managers and operators should also strengthen inspection and sampling to ensure that in the production process, products beyond the reasonable range of color difference can be found and processed in a timely manner.
With the development of printing detection technology, the accuracy of color difference detection equipment has also been greatly improved. Conditional printing enterprises can introduce relevant color difference control equipment to achieve digital color difference management.
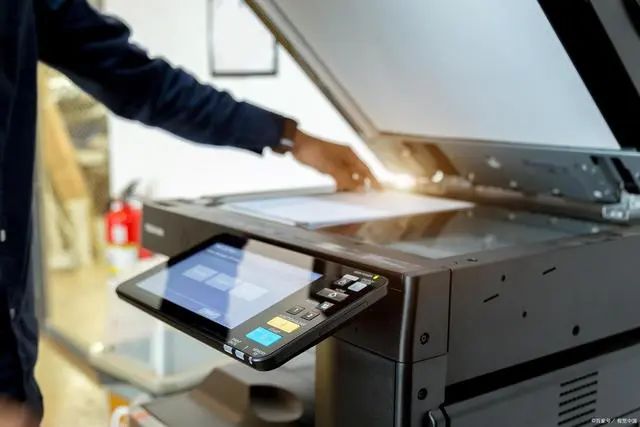
Equipped with printed standard light source
Some printing companies do not use printing standard light sources, which brings hidden dangers to the color consistency control of printed products. The product color seen under the lighting source during the night shift is very different from the product color seen under the daylight during the day shift, which is easy to lead to printing color differences. Therefore, it is recommended that the printing workshop must use the printing standard light source for lighting, and if necessary, it is also equipped with a standard light source box.
Ensure the quality of printing ink
Printing companies sometimes encounter such a situation: after the printing product is placed at the customer‘s place for a period of time, the ink color gradually changes, but the same phenomenon does not occur in the first few batches of printed products. This is usually due to the use of expired ink. The shelf life of ordinary ink is usually one year, and the use of expired ink is easy to fade the printed product. Therefore, in the use of ink must pay attention to the ink shelf life, adhere to the principle of first in first out. In addition, in the printing production process, but also pay attention to the amount of ink additives. If the ink additive is used too much, it may also cause the color of the ink to change after printing. Therefore, when using various ink additives, it is best to communicate with ink suppliers to determine the correct proportion of additives.
Pay attention to the ratio of spot color ink and information transmission
In the process of printing production, spot color inks are often prepared, and the printing workshop preparation of spot color inks often appears that the color of the matched ink is far from the sample color. The main reason for this kind of situation is that the ink ratio is wrong. Spot color inks are prepared by a variety of primary inks, and most primary inks are pantone colors, so when we prepare spot color inks, we often prepare them according to the ratio given on the Pantone color card. However, it should be pointed out that the ink ratio on the Pantone color card is not necessarily completely accurate, and there are often small differences. This has certain requirements for the experience of the operator, requiring it to have a high sensitivity to the ink color, requiring it to learn more and practice, constantly accumulate experience in spot color ink configuration, improve color sensitivity, and achieve the level of proficient ink configuration. Here I would like to remind you that not all primary inks are based on the Pantone color system, and when encountering non-Pantone primary color inks, it can not be determined by the ink ratio on the Pantone color card, otherwise it is difficult to formulate the required ink color.
In addition, in order to ensure the accuracy of the spot color ink ratio, many printing companies are equipped with electronic scales, which is worth advocating (it should be noted that the electronic scale should be calibrated regularly). Standardization is one of the important measures for the progress of industrial production. Our practice is that when the spot color ink is prepared for the first time, the operator will record its ink ratio on the process card and "quality record" in order to provide basic data for the next preparation of the spot color ink, but also to ensure the consistency of the color of the spot color ink prepared by different shifts and different operators.
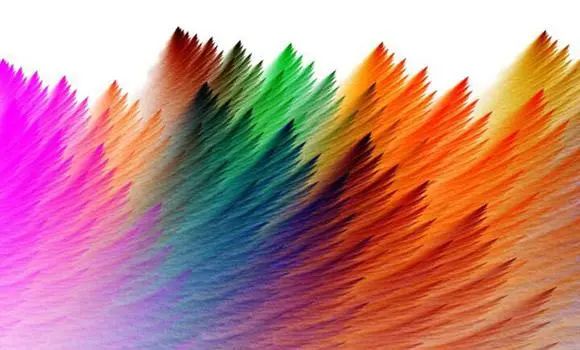
Make a suitable plate
We often encounter such a situation: the color of the product printed when tracing the sample is far from the color of the sample provided by the customer. This situation is mostly caused by the dot density and size on the plate and the sample dot density and size is different, it is recommended to follow the following steps to improve.
First of all, use a special cable ruler to measure the number of sample plus cable to determine the number of plate plus cable consistent with the number of sample plus cable. This step is crucial.
Secondly, the magnifying glass is used to observe whether the dot size on the color plate is consistent with the dot size of the corresponding color of the sample. If not, it needs to be adjusted to the same or approximate size. It should be noted that because the dot after printing will increase, so the size of the dot set when making the plate is slightly smaller than the dot on the sample.
Finally, observe whether the printing ink hue is consistent with the sample ink hue.
Under normal circumstances, the above three points can be achieved, and the color of the printed product can be basically the same as the color of the customer‘s sample, and the difference will not be too large.
Fully evaluate the impact of surface treatment processes on the color of printed products
In the printing process, this situation is often encountered: when printing, the color of the printed product and the sample color are very similar, but the color changes greatly after the film is coated, especially after the surface is coated with matt film, the color difference is greater. This situation must not be careless, especially in the printing of dark blue series and red and yellow series colors, it is best to do a film coating test before the formal production, adjust the printing color according to the effect of the film coating, and save the uncoated printing sample for subsequent production comparison. In addition, the calender process also has a great impact on the deep blue series of color blocks, which should be considered in advance when printing.
Master the discoloration rule of special color after drying
Printing colors are changeable, some colors at the beginning of printing, and the color of the sample is very close, but after drying, it is very different from the color of the sample, especially when printing with the dark blue ink deployment of light blue ink, the red situation is obvious after drying, and must pay attention to printing.
In addition, metal inks such as gold and silver, due to the composition of the ink, its monochrome or spot color ink with its deployment will also change after drying. At the same time, the color effect of the printed product is greatly affected by the observation Angle, so when printing with this ink, it is necessary to understand the customer‘s observation environment in advance, whether it is in the daylight or under the light, and try to be consistent.
The printing process is a dynamic balance process, each stop will cause color difference. Therefore, the unity of printing color has become an important printing quality indicator. Many of these tips are long-term accumulated experience in the printing process, and I hope the above experience will help the industry peers better control the printing color and print more personalized and attractive products.